Multi-Material Multi-Method (M4) 3D Printing
The advent of additive manufacturing (AM), also often referred to as 3D printing, has enabled the rapid production of parts with complex geometries that are either labor-intensive or unrealizable by traditional manufacturing methods. Many existing 3D printing technologies, however, only allow one material to be printed at one time, while many applications require the integration of different materials, which sometimes cannot be printed by one AM technology. In this paper, a novel multi-material multi-method (m4) 3D printer comprised of multiple AM technologies is presented as a solution to the current limitations. This printer fosters the advancement of AM by combining materials traditionally unable to be printed concurrently while adding functionality to printed parts.
4D printing of active composites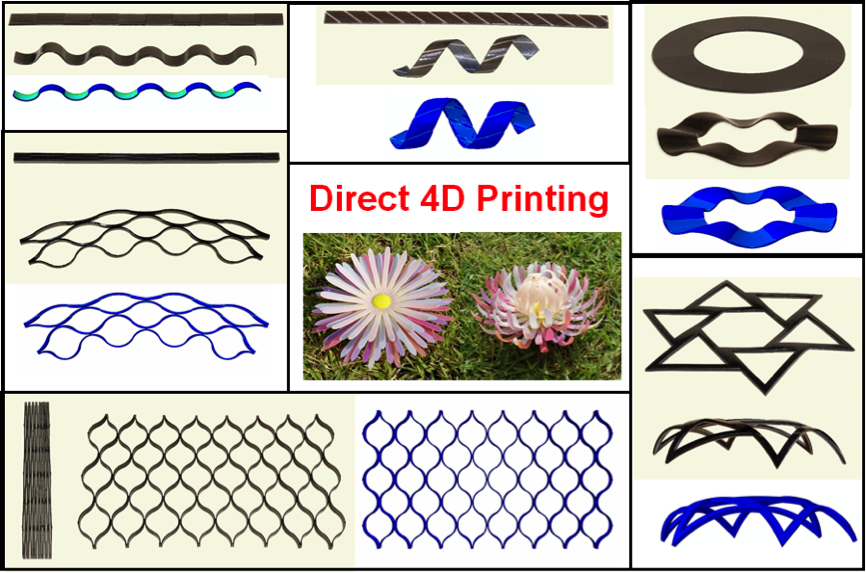
Recent fast advance in 3D printing technology makes it possible to print multiple materials simultaneously and thus enables to create composites with controlled inhomogeneities with desired properties. In this research, our focus is to create active composite, which can change its shape after 3D printing; the shape change is controlled by external stimuli and is a function of time, the 4th dimension aspect of this new paradigm. Research efforts include understanding properties of existing materials, developing material models and applying models to active composites design.
The above video show the “Printed Origami”: the printed sheet folds into an origami airplane. Note: the water used here is for temperature control. Videos by Dr. Qi (Kevin) Ge and Mr. Conner Dunn.
Photonic curing of conductive metallic inks on 3D printed soft materials
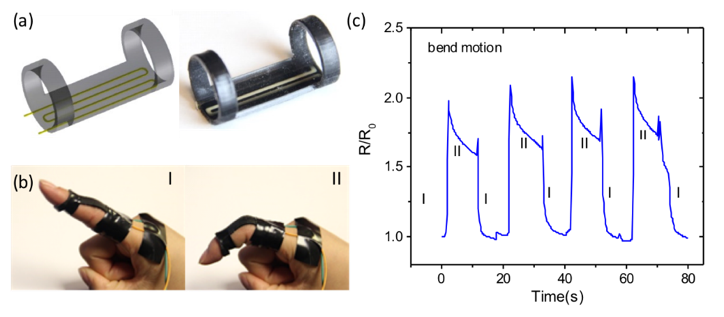
In this research, we study the physics and mechanics of curing conductive NP inks on 3D printed substrates by different methods, especially the photonic curing method, which will be integrated with our hybrid 3D printing system. We investigate how the curing conditions (energy input, substrate temperature etc) to the electromechanical properties of the printed NP inks, such as conductivity, adhesion, wire stretability and fatigue behaviors, and substrate damage. We are also interested in combining inkjet printing, DIW and 3D printing to fabricate all printed smart device.
Recycling thermosetting polymers
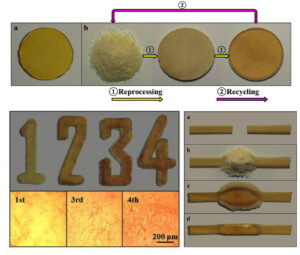
Network polymers are often called thermosetting polymers because the covalent bond formed network are stable even at high temperature. They offer the desired high temperature stability feature but also create trouble in handling their waste, as they cannot be easily reshaped and reused as thermoplastics. Recently, this has been changed by the introduction of a new group material called covalent adaptive network (CANs) where the bond exchange reaction can release the stress without changing the overall structure of the network. In this project, we study the molecular mechanism of bond exchange reaction and apply our understanding to the reprocessing and recycling of these polymers. The photos on the right show the reprocessing procedure from epoxy powders to epoxy bulk material (top), (bottom-left) for multiple times; In addition, the epoxy powder can be used to reconnect two broken parts (bottom-right). Photos by Dr. Kai Yu.
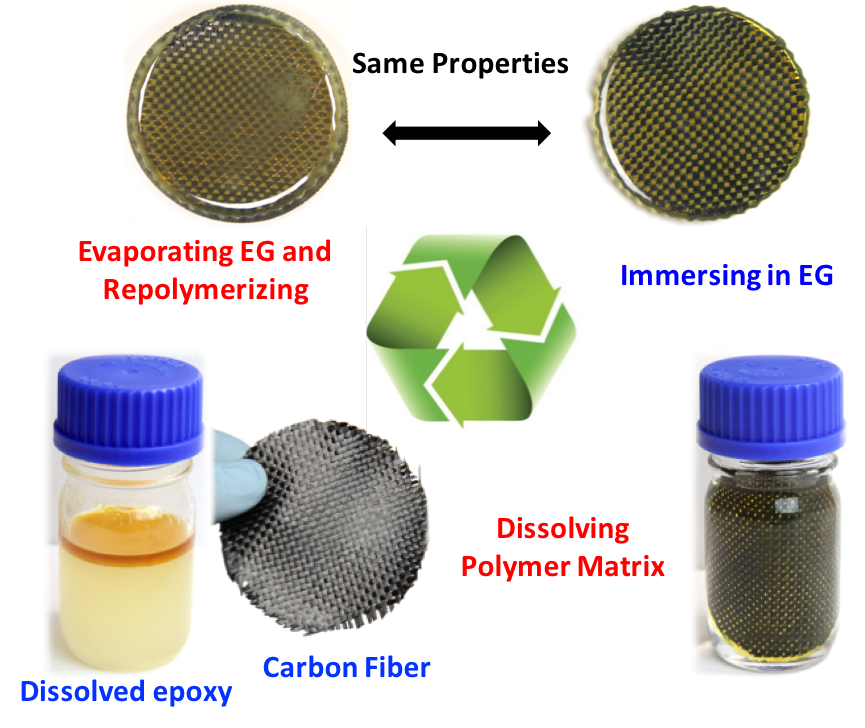
More recently, we extended this work to 1) recycling carbon fiber composites; and 2) recycling 3D printing of epoxy vitrimer. The figure on the left shows that carbon fiber composites can be recycled by using EG. Here, not only we can retrieve the carbon fabrics, but also we can collect the matrix epoxy and reuse it. Therefore, this is a truly near 100% recycling.
This approach is further used to 3D printing the thermo-setting epoxy. Our achievements are: 1) we can print hollow structures and thermally cure the thermosetting epoxy without crashing it; 2) we can recycle in the ink the use it multiple times; 3) the surface the printed part can be repaired using our ink materials.
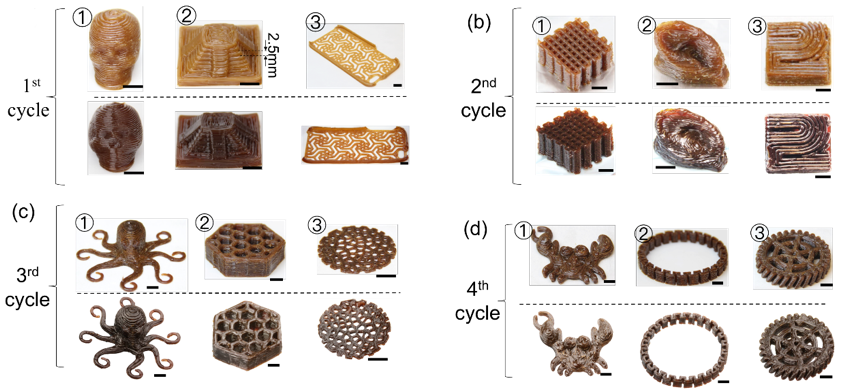
Smart Fabrics
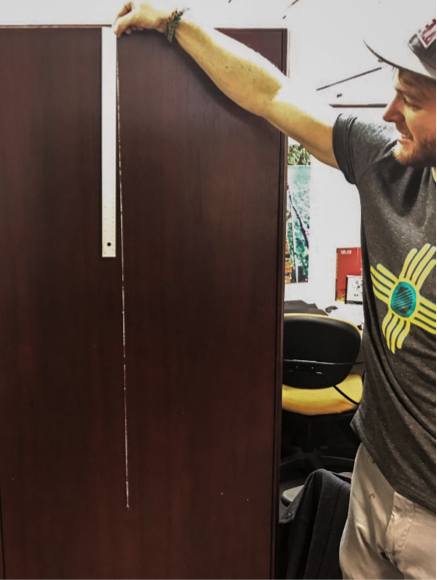
This research focuses on developing smart fibers for use in smart clothing able to actively respond to the wearers environment as well as monitor their performance or health. Recently we have been utilizing the programmable, two-way actuation property of liquid crystal elastomers (LCEs). When LCE is exposed to increased temperatures, it will shrink but will return to its original size when cooled back down. We have developed a new technology to make long LCE fibers and weaving them into textiles, we can achieve smart clothing that will respond to the wearers temperature to allow a more breathable shirt. The video below demonstrates this concept with woven LCE fibers. We hope to establish the connection between the processing and printing conditions of the LCE and the final fiber parameters such as diameter, strength, and activation strain.
3D Printing of Papers
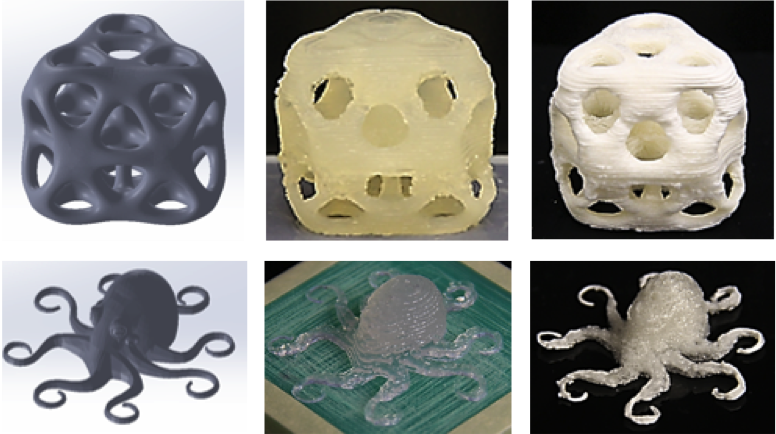
Cellulose nanocrystal (CNC) and cellulose nanofiber (CNF) aerogels with controlled 3D structures are printed using the direct ink write (DIW) technique. DIW 3D printing followed by freeze drying can produce cellulosic aerogels with minimal structural shrinkage or damage. A processing strategy for making cross-linkable TEMPO-CNF hydrogel ink that is suitable for DIW processing was also developed. The resultant cross-linked aerogel 3D structures are extremely light weight, stable under water environment, and can be cyclically compressed in water without structural collapse. The resultant aerogel structures have great potential in applications such as tissue scaffold templates, drug delivery, packaging, etc., due to their inherent sustainability, biocompatibility, and biodegradability.
Mechanics of shape memory polymers
Shape memory polymers (SMPs) are a class of soft active materials that can change its change upon external stimuli on demand. Because of SMPs’ many advantages over conventional active materials, such as low-cost, large shape change, and good biocompatiblity. SMP research is one of the most active topic areas in functional materials. Since 2005, our group has been working on SMPs with the goal of developing mechanistic constitutive models that can be used to assist simulation based design. Through extensive thermomechanical characterization experiments, we developed two classes of constitutive models: one is based on thermoviselasticity and the other one is based on phase evolution in soft active materials. Current research in SMPs includes developing constitutive models for new SMPs, connecting continuum level modeling with macromolecular level understandings, application design based on simulations, etc.
The video bellow shows an ABAQUS FEM simulation of an SMP stent where it is folded at high temperature and stored in the folded shape by cooling and later recovers its tube shape. The color in the stent represents the temperature. (Video by Dr. Kristofer Westbrook)
Mechanics of Photomechanical Properties of Polymers and Photo origami
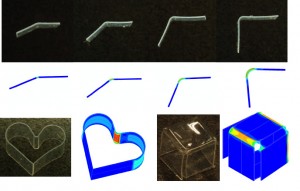
Origami is an ancient art of paper folding that can be found in China, Japan, Spain, etc. In modern days, origami not only evolves into a combination of art and math that inspire many of us since kids, but also offers solution to many challenging technical problems such as packaging. In this project, we will utilize the recent advance in polymer development where light irradiation can change the structure and thus the mechanical state of polymers and develop a new paradigm of material folding — photo origami. Whilst developing constitutive models for materials that interact with light are an intensive efforts in our group, we are also interested in pursuing the novel design of photo origami. The photos on the right show a heart and a box that were folded from flat sheets by light irradiation. (Photo sources: experiments: Ms. Jennie Ryu and Mr. Matteo D’Amto, FEM simulations: Dr. Xiaodong Cui).